Eckart Bünning berichtet von präziser Handarbeit in der ehemaligen Gießerei Hinsch (Am Krähenwald 24). Eigenes Erleben wurde mit Erzählungen vom Ehepaar Blanken, Tochter und Schwiegersohn des inzwischen verstorbenen Bruno Hinsch, ergänzt.
„Aus meiner Tätigkeit als Schornsteinfeger kann ich mich gut an die Werkstatt von Bruno Hinsch erinnern. Die Siedlung Hinschendorf gehörte nämlich von 1940 bis 1943 und dann nach dem Kriege von 1946 bis 1952 zu meinem Arbeitsbezirk. Wir suchten zur Mittagspause warme Räume, wo wir unser Brot essen konnten. Gaststätten waren um diese Zeit noch geschlossen und außerdem kosteten die Getränke Geld, das immer knapp war. In so einer Siedlung wie Hinschendorf war die Auswahl nach warmen Räumen nicht groß. Neben dem Treibhaus der Gärtnerei Bruns im Kreutzkamp 13 blieb nur noch die Werkstatt Hinsch.
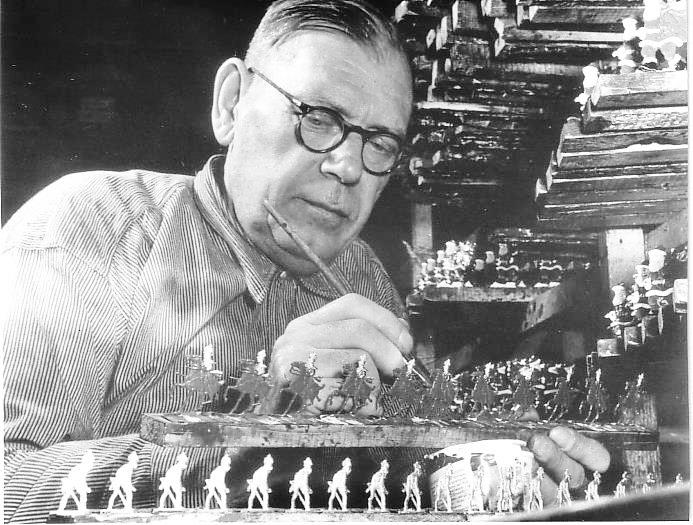
Bruno Hinsch bei der Arbeit. Foto: Familie Blanken.
Ich habe gerne dort gesessen und dem Meister bei seiner Arbeit zugeschaut. In einer Ecke des Raumes stand ein runder Herd auf hohen Füßen. Ein Dunstfang war darüber angebracht, der den Rauch und die Zinndämpfe abführte. In einer runden Öffnung der Feuerplatte stand der Tiegel mit dem geschmolzenen flüssigen Zinn. Es glänzte silbrig, und wie kleine graue Inseln schwammen ein paar Schlacken auf der Oberfläche. Links vom Ofen stand der Arbeitstisch. Seine Oberfläche war mit Blech und Asbest beschlagen. Eine runde Petroleumlampe stand auf dem Tisch. Sie hatte allerdings keinen Zylinder und diente auch nicht zur Beleuchtung. Sie sollte vielmehr ein wenig Ruß erzeugen, mit dem die Formen bei ihrer Herstellung geschwärzt wurden.
Vor Ofen und Tisch saß Bruno Hinsch auf einem Stuhl. Mit seiner rechten Hand fasste er eine kleine stabile Schöpfkelle, mit der er flüssiges Zinn aus dem Tiegel nahm und in die Form goss. Die Form hielt er in seiner linken Hand, die er auf dem Tisch abstützte. Weil sie mit der Zeit sehr heiß wurde, trug der Meister zum Schutz seiner Hände dicke Lederhandschuhe. Das flüssige Zinn wurde nun langsam in die trichterförmige Öffnung der Form hineingegeben. Es war schnell abgekühlt, und nun konnte schon die Form geöffnet werden. Mit einer Zange wurde die Zinnfigur herausgenommen. War sie zur Zufriedenheit des Meisters ausgefallen, kam sie auf den Tisch zur Weiterverarbeitung. Fehlerhafte Figuren kamen zurück in den Zinntiegel und wurden erneut eingeschmolzen.
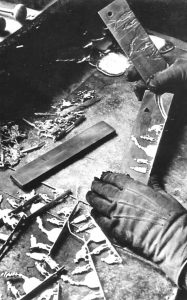
Öffnen der Formen. Foto: Familie Blanken.
Eine Gießform bestand aus einem sehr feinen Schiefer, der fertig auf Größe geschnitten aus Thüringen kam. Drei Steinplatten waren für eine Gießform erforderlich. Ein Oberstein und ein Unterstein für die Seiten und ein weiterer Stein als unterer Abschluss für den Fuß.
Die Figuren hatte Meister Hinsch eigenhändig entweder nach gekauften Vorlageblättern oder nach eigenen Entwürfen gestaltet. Mit viel Geduld und Können wurde in präziser Handarbeit die Figur plastisch in den Formstein eingearbeitet. Feine Stichel und Schaber waren sein Handwerkszeug. Die Figuren wurden gleichermaßen in den Ober- und in den Unterstein eingearbeitet. Dabei mussten beide Figuren des Formenpaares ganz exakt übereinander liegen. Ober- und Unterstein wurden aufeinandergelegt und fixiert und dann beide Steine durchbohrt. Die Bohrlöcher von 8 Millimeter Durchmesser wurden mit flüssigem Blei ausgegossen. Nach dem Erhärten blieb in einer der Formhälften ein Bleidorn stehen, der genau in die Bohrung der andern Hälfte passte. In die untere Formhälfte wurde zunächst der Umriss der Figur eingeritzt. Die so gravierte Hälfte wurde mit dem Ruß der Petroleumlampe geschwärzt, worauf die beiden Formsteine fest gegeneinander gepresst wurden. Der Ruß war so auf die unbehandelte Hälfte übertragen, die Figur ist deutlich sichtbar und konnte ausgearbeitet werden. Passte alles präzise zusammen, konnten die Figuren plastisch in die Formsteine eingearbeitet werden.
Nicht nur die Figur wurde eingeritzt, vielmehr mussten auch viele feine Lüftungskanäle angelegt werden. Sämtliche Luft musste beim Gießvorgang aus der Form entweichen und durch Zinn ersetzt werden können. Ein falsch angelegter oder verstopfter Luftkanal führte zu einem Fehlguss. Ein größerer trichterförmiger Kanal diente zum Eingießen des flüssigen Zinnes.
Der Fuß der Figur lag am Außenrand der Form und wurde durch einen besonderen Stein abgedeckt. Das System war so ausgeklügelt, dass mit einem Gießvorgang in einer Form gleichzeitig mehrere Figuren hergestellt werden konnten. Die Figuren waren hintereinander eingraviert und durch Kanäle miteinander verbunden.
Über dem Koksfeuer im Herd stand der Tiegel mit dem flüssigen Zinn, einer Zinnlegierung, deren Zusammensetzung als Betriebsgeheimnis gehütet wurde. Reines Zinn ist für die Herstellung von Figuren zu weich.
Vor dem Eingießen des Zinns wurde die Form kurz über die Flamme der leicht blakenden Petroleumlampe gehalten. Es bildete sich auf der Form ein hauchdünner Rußfilm. Die fertigen Figuren lösten sich dadurch besser aus der Form.
Wenn eine große Stückzahl aus einer Form hergestellt werden sollte, wurde anstelle von Ruß ein Pulver aus dem Samen von Bärlapp verwendet. Eine Form konnte für bis an die tausend Gießvorgänge benutzt werden. Durch die Hitze platzten mit der Zeit feine Splitter ab. Die Qualität der Figuren wurde den hohen Ansprüchen nicht mehr gerecht und nun musste eine neue Form hergestellt werden.
Wenn am Nachmittag das Feuer herunter gebrannt war, wurden die am Tage gegossenen Figuren abgeputzt, entgratet, wie der Fachmann sagt. Es waren noch Nähte und Ansätze der Luftkanäle an den rohen Figuren. Mit einer scharfen Zange oder einem spitzen Messer wurden die Überstände abgeschnitten und die Ränder geglättet. Ein kleiner Teil der fertigen Figuren wurde so, blank und unbemalt, an Sammler verkauft, die sie nach ihren eigenen Vorstellungen bemalen. Der weitaus größere Teil der Rohprodukte wurde jedoch hier in der Werkstatt nach traditionellen Vorlagen bunt bemalt.
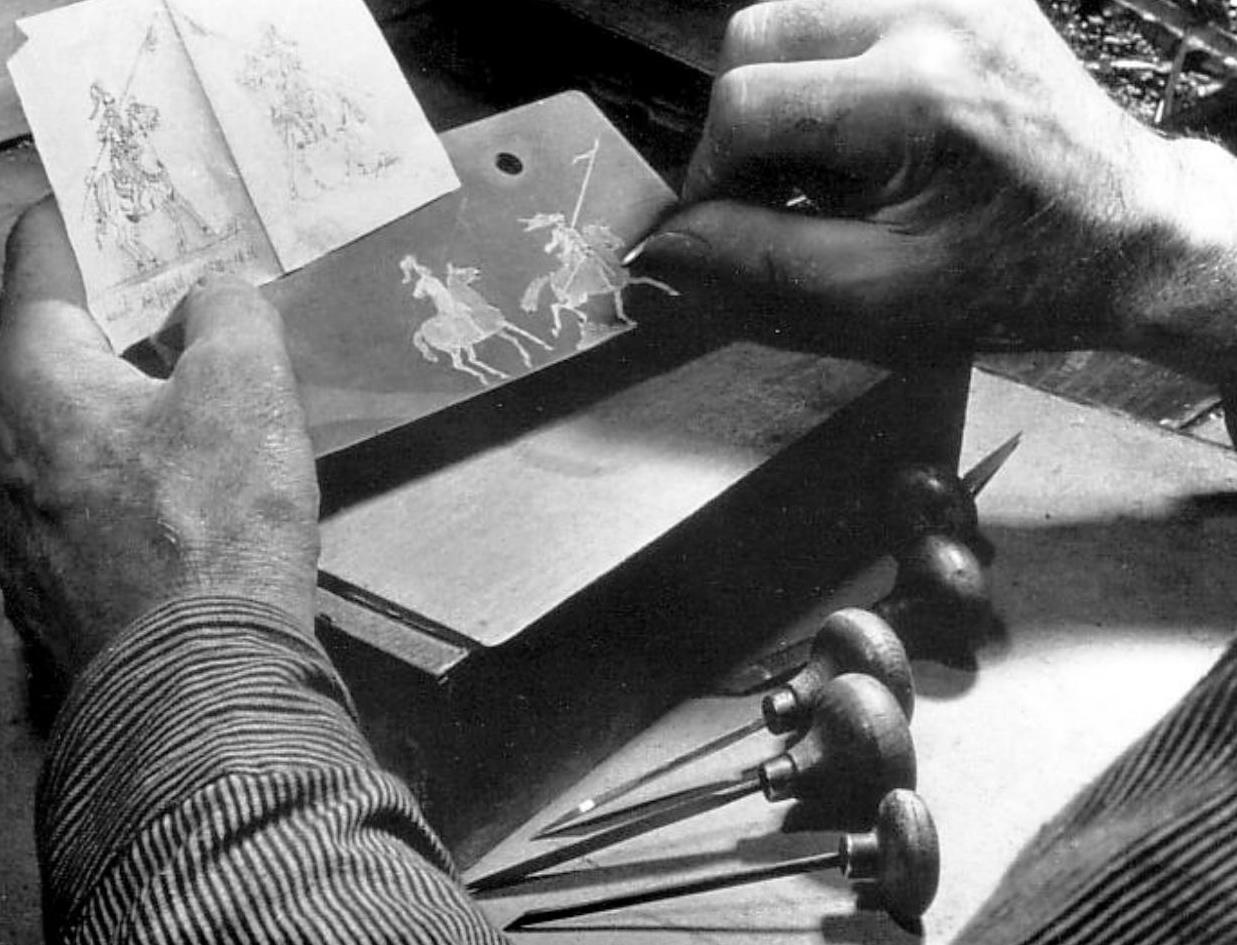
Foto: Familie Blanken.
Dazu wurden die Figuren in eine etwa 45 cm lange Leiste geklemmt. Mit einem feinen Pinsel wurde die Ölfarbe aufgetragen. Häuser und Tierfiguren erhielten Farbe nach der Vorstellung des Malers. Volkstrachten und Uniformen mussten jedoch exakt dem Vorbild entsprechen. In einer Sammelmappe bewahrte Meister Hinsch die postkartengroßen bunten Vorlagen auf. Die Bemalung wurde wie am Fließband vorgenommen. Auf der Leiste standen 10 bis 20 gleiche Figuren nebeneinander. Der Reihe nach wurde punktuell die gleiche Farbe aufgetragen. Dann folgte die nächste Leiste. Erst wenn die eine Farbe trocken war, begann man in gleicher Weise mit der nächsten. Nach einem abschließenden kritisch prüfenden Blick des Meisters wurden die fertigen Figuren zum Versand in einen kleinen Karton gelegt und durch Wellpappe gesichert. Ein Etikett mit Angaben zu Inhalt und Herkunft wurde aufgeklebt und der Versand an Spielzeughändler oder Fachgeschäfte konnte erfolgen.
In den Jahren nach 1950 wurde ein großer Teil der Produktion aus der Werkstatt Hinsch nach Amerika exportiert. Ein weiterer Gießer war eingestellt worden und in den Kellerräumen waren mehrere Frauen und Mädchen mit der Bemalung der Figuren beschäftigt.“